Why you need to get PAT testing done
Lets get started by dealing with the elephant in the room – you DO need to get PAT testing done. Let us tell you why… if you have an accident at work (or in any place of work), and that accident is caused by faulty electrical equipment, e.g. a fire, electric shock, etc. then the accident investigators are going to want to see proof that the equipment was maintained and safe. If you can’t provide that, then you are in trouble.
If an electric heater catches fire, an extension lead overheats, a damaged cable gives someone a shock, and you are sued, you need to be able to prove you did everything possible to ensure the appliance was safe.
If you have risk assessments in place, and up to date PAT Testing Certificate reports showing those appliances, then you have some evidence that you have done everything you can to ensure that the equipment was safe. However, that evidence needs to back up that you have done everything – that means you have had the equipment checked recently enough to be considered an acceptable timeframe, and that users of equipment are encouraged to report new faults. Don’t think because it was PAT Tested 5 years ago, that that is enough.
Regular PAT testing; that is annual PAT testing, for most common workplaces is considered best practice and preferred by insurance companies. In some places testing should be carried out more often (such as building sites) and in others a less often frequency can be considered (e.g. offices with fixed equipment that never moves); but don’t try to decide that yourself – let us guide you; after all we are PAT testing experts!
You must comply with the The Electricity At Work Regulations
The Electricity at Work Regulations (which is the guidance you should follow) require all workplaces to ensure electrical equipment provided for use at work (which also refers to home-workers and equipment in other business premises such as rental properties) is safe to use at all times, and requires you as the ‘duty holder’ of a ‘business’ to ensure that equipment maintains the required safety standards at all times.
How you do that is up to you, but the most recognised method, and generally the best option is what ‘we’ call PAT Testing. In full, Portable Appliance Testing which covers all electrical items fitted with a plug, is carried out to check and confirm that the item is safe, or to repair it, or remove it from safe, thus removing the risk of accident.
The electrical industry refers to the process as Electrical Equipment Testing (EET) because some appliances have been missed in the past, because business owners have ‘hard wired’ their appliances to the mains. This was done by an electrician, who took the plug off, and fed the flexible cable into a fused connection unit (white plate on the wall with a fuse and switch usually), hard wiring it to the mains wiring. Some of these items should only be checked by specialist engineers, but those that started life with a plug on should also be included in the PAT testing (although need someone competent to inspect them).
About the PAT testing service we provide
For sake of argument, and for understanding. We call the process, PAT testing. We know it’s not strictly correct, but it is the term everybody uses, so that’s why we call it that.
For us the process involves:
- Working with you to ensure minimal disruption to your business whilst we conduct our inspections.
- Checking all electrical equipment fitted with a plug now, or intended by the manufacturer to be used with a plug fitted (including appliances that have had the plug removed and been hard wired)
- Visually inspecting all parts of the appliance from the plug to the main unit, checking inside the plug and the full length of the flexible cable.
- Visually checking the socket the item was plugged in to, and advising you of any faults (others charge for this, we don’t).
- Carrying out any necessary repairs on the equipment to ensure it is safe to use, including repairing the cable, the plug, replacing the plug and or fuse (all free)
- Carrying out any electrical tests appropriate to the appliance, to check it is internally safe, such as checking for earth protection continuity, insulation and polarity in leads.
- Carrying out cable management where possible – i.e. tidying up messy cables and recommending ways to improve cable management.
- Assessing whether the equipment is suitable for the task, the environment and recommending ways to improve safety, and providing guidance on retest periods. We also check to see if the appliance is genuine or counterfeit (where possible).
- Labelling each appliance, with labels we print inhouse, that include a unique identification number that directly relates to the report we provide you with.
- Recording each appliance’s description, results, and location, in our database, which is provided to you in an itemised report.
- On completion of the job, our engineer updates you on everything that has been done, anything you need to be aware of, any concerns or feedback and asks you to do a Google review of our work. He will also discuss retest periods with you and recommended frequencies for next inspections (we can also discuss this with you separately in meetings/zoom/telephone etc.
- Our engineer completes a ‘job record form’ to confirm the job is complete, which is sent to the office and a copy to you.
- The invoice will be raised and sent by email, for payment on receipt, or within an agreed timeframe. Our standard credit term is 14 days, but this can be extended on request.
- At the end of the day or on Friday afternoon our engineers complete their admin, producing your PAT Testing Certificate Report, which is sent to you as a PDF document. This document includes everything you need, including test results (many companies don’t provide electrical test results, but you will need them if ever investigated).
- You will be added to our system for repeat bookings – when you are due a new inspection, we will send you a reminder. We plan this by booking you in for next time, now, and reminding you of that date about 8 weeks in advance. That date can be changed if not convenient.

Equipment included in the PAT testing process
Every part of the appliance is checked – All mains powered detachable, individual parts of the appliance need checking. Basically, if you unplug it and it stops working, then it is electrical equipment, and for purposes of danger prevention, it needs to be checked. This includes the mains wire (cable), any power switching devices (usually little black rectangular boxes attached to the cable), and the unit itself. Each of these is counted as an ‘item’ of electrical equipment. Each is inspected, and where necessary, tested. Each is labelled and recorded for the report.
Extension Leads – all extension leads, cable reels, etc that supply power are included in our inspections. The full length of the cable will be checked and any damage repaired.
Fixed Appliances – We carry out our inspections and tests on all types of electrical equipment that was intended by the manufacturer to have a plug – this includes any items that now don’t have a plug. These are called fixed appliances.
Fixed appliances have had the plug removed and the cable hard wired to the mains. This generally includes water boilers, heaters on walls, some televisions, hair dryers in hotels, etc. We also include integrated kitchen appliances where the plug can’t be accessed. Appliances that were never intended to have a plug, are not included – these generally are the ones you have service plans for.
A full inspection of the appliance, involves removing the cable from the mains, which should only be done by a competent person or electrician; we can do this, not all PAT testers can. We don’t do a full inspection as standard, because the power needs turning off, but it can be arranged. For more information see our fixed appliance testing page.
When we come across fixed appliances, whilst checking those with plugs, we do the best inspection we can. This always involves a visual inspection and in the case of ‘class 1’ appliances, we will conduct an earth continuity test between the socket circuit and the appliance.
Microwave Emissions Tests – Microwave ovens are slightly different to most other electrical appliances, in that as well as being powered on when plugging in, and providing an electrical safety risk, they also emit micro-wave radiation, which is an added risk that needs to be checked. So we check the door lock function works correctly, that there is not too much internal rust build up and that the micro-waves do not leak out of the door seal too much. More information is available on our microwave emissions page.
Equipment with Commando Plugs – commando plugs are the ones that look different to normal plugs – they are usually coloured yellow, blue or red, and are intended for use on building sites or where 230v would be considered too great a risk, so 110v (yellow) systems are used.
Blue 230v adaptors are used for equipment that needs higher protection than a 13amp fuse, such as for some commercial kitchen appliances and in factories, and in environments where higher voltage or 3-phase electricity is used we have red 415v plugs. These all have to be inspected as part of the PAT test.
Please note, these are not standard, and so command higher charges for the inspection and test, and may incur charges for repairs, however, we always check with you before doing chargeable repairs.
Server Systems – everyone is terrified that their server won’t turn back on; we never turn them off. If you want to, that’s up to you, but we don’t. We will do the best inspection we can, visually, of every part, and where possible do a check with a thermal image camera (they’re expensive, not all our engineers carry them). This means your server is included in the equipment log, but as it has not been unplugged we can’t check the plug meets the standards, so we recommend a full shutdown be arranged, at least once every 5 years. More information on Server System PAT testing.
What you get from PAT Testing
As well as peace of mind that your electrical equipment is safe, you also get a document that acts as evidence that you have done your duty to ensure your electrical equipment is safe; that is called the PAT Testing Certificate. It is a report that references the inspections carried out, and the results obtained.
Minimum industry standards require the report to include confirmation the appliance has passed, so a report with ‘Pass’ on it, is sufficient. The report will list the appliance, the test date, the engineer and that it passed.
However, a minimum standard report will not protect you in a legal dispute. For that you need real results that have meaning, so you need what we provide as standard (most PAT companies do not provide this):
- Electrical test readings for every appliance tested, that clearly show that the reading achieved is within the parameters of acceptable readings in British Standards; and where not, reasons given why.
- What repairs were carried out and what parts were supplied
- Why failed appliances failed their inspections and recommended actions.
With these 3 items on the report, you are much better protected.
When we test an appliance we record the test results and show them on the report (unless you tell us not to), if we carry out a repair we record it on the report – that’s an essential maintenance log of preventative maintenance.
About our PAT Testing Service
Our engineers are highly trained, qualified and competent to inspect and test electrical equipment. We also have passed DBS checks. Staff undergo regular Health and Safety training and hold CSCS cards.
All items are tested in accordance with the latest British Standards, PATTA and IET guidance.
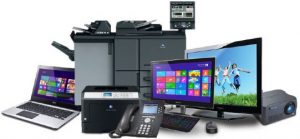
- Regular tests help you maintain safe electrical equipment
- The engineer assesses the suitability of an appliance for the environment it is being used in to help you comply with The Provision and Use of Work Equipment Regulations 1998
- PAT testing records can be used to demonstrate compliance with the Electricity at Work Regulations 1989
- Regular PAT testing helps you to comply with The Workplace (Health, Safety and Welfare) Regulations 1992
- Regular PAT tests in rental property help you comply with The Housing Act 2004 (England and Wales)
- PAT tests before the start of a tenancy help a landlord comply with The Ministry of Housing, Communities and Local Government’s guidance
- Regular PAT tests help you comply with The Electrical Equipment (Safety) Regulations 2016
- PAT testing finds plugs that don’t meet the Plugs and sockets etc. (Safety) Regulations 1994 and corrects it.
There are 10,000% more counterfeit electrical goods in the UK now than 20 years ago
Our engineers are fully aware of counterfeit goods and we’re always updating our knowledge of them, so if you them, we can spot them. Counterfeit electrical appliances, such as fake Apple chargers, or the fake ‘Lenovo’ laptop charger in these photos, are a major fire risk and have been proven to be the source of many domestic fires.
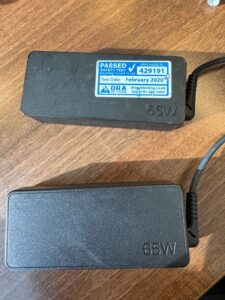
The top charger is genuine, the bottom is ‘fake’. Lenovo is a creditable brand in the IT industry producing some fine IT equipment, but buying a replacing laptop charger can be expensive, so people turn to online retailers for a cheaper option. This find, imported into the UK market is not a genuine Lenovo item, although through its embossed printing and design, is being passed off as such. This is an example of a counterfeit appliance.
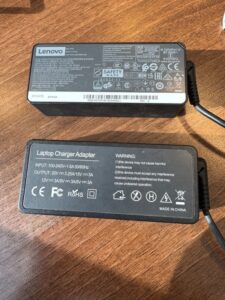